
Ortlinghaus is leading specialist for the supply of clutches, brakes, plates, and compact drives including hydraulic power packages and control units. Our global network, consisting of more than 25 branch offices, sales partners, and service points, ensures that we can respond quickly and stay in touch with our clients' needs.
Ortlinghaus Plates
Ortlinghaus Brakes
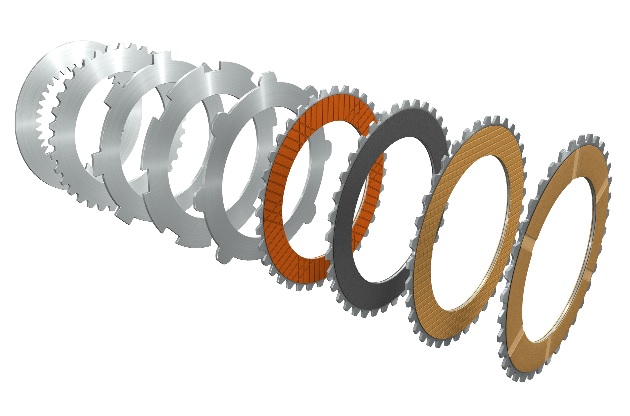
For dry- and wet-running clutches and brakes, Ortlinghaus is able to provide a very comprehensive range of plates. The plates and the friction surface are important functional elements in every clutch and brake, and have been developed in many different ways since the early days of clutches and brakes. The choice of friction system depends on the application: in general, one plate with friction material works together with a counterplate of steel or cast iron. The inner and outer plates are mounted with the other drive components by lugs and slots, and the spline is in accordance with DIN 867 and DIN 5480 as well as other standards. In addition, holes in the plate for studs and special shapes in accordance with customer requirements are available. Combined with a multi-plate clutch or brake, these plates come in a multitude of different dimensions, friction combinations, and surface patterns.
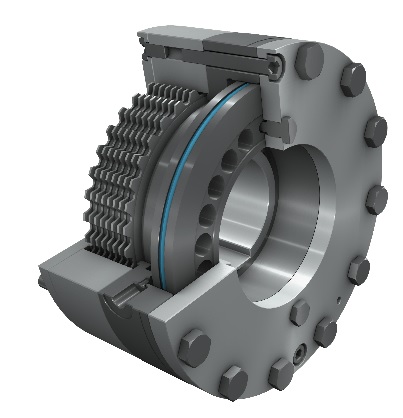
The 022 series is one of the most successful Ortlinghaus products. Well over one million units are in service around the world wherever safety brakes with an extremely long service life and quality without compromise are required. In mining equipment engineering, these multi-plate brakes are used in travel/drive brake and slew drive brake applications. The advantage of these wet-running, hydraulically released and spring-applied multi-plate brakes is the high torques they achieve in compact dimens
Ortlinghaus Clutches
Clutch-brake units
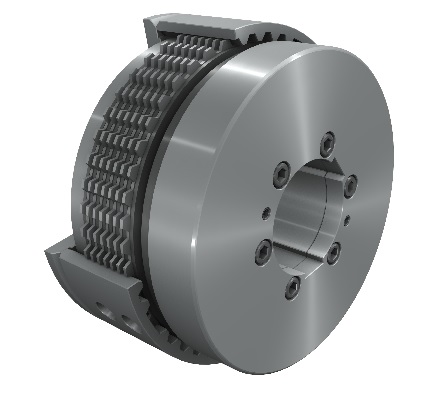
Based on our friction linings, which have been tried and trusted for many years in the marine sector, clutches in this series reconcile high torque and thermal absorption rates as well as a favorable outer diameter. A high shaft diameter can also be used. Due to their broad power spectrum, smaller sizes can be achieved with corresponding weight and cost benefits, especially in higher torque ranges. The optimized outer diameter makes shorter distances between axles possible, and in this way offers clear savings potential in the gearbox. The hydraulic multi-plate clutch impresses with its
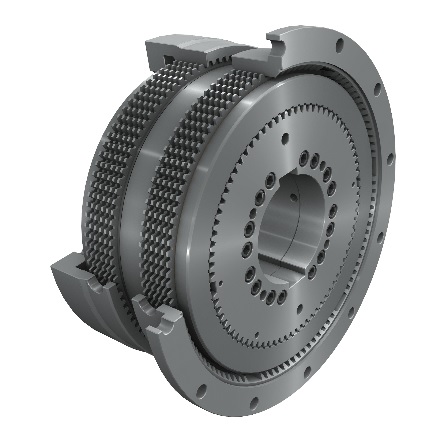
The hydraulically actuated clutch-brake units from the series 123 work exclusively with wet-running, oil-cooled plates with friction pairing steel/sinter.
The advantages of having a multi-plate construction and oil-cooled friction pairing steel/high-performance sinter in addition to actuation with pressure oil at 60 bar are seen in the product’s extraordinarily compact design and high operating efficiency. The series offer high torque, low moment of inertia and high switching speeds with a minimal need for maintenance. Model series 123 represent a good alternative to dry-running combinations. They operate in sealed housings which prevent leakage and keep switching noise to a minimum.
With these benefits, the clutch-brake units are suitable for a broad range of applications in press, shear press, and large press engineering as well as in embossing presses and drawing presses.
The series was designed and constructed according to international safety regulations and approved by the German employers’ liability insurance association.
Mechatronic Systems
Mechanical Systems
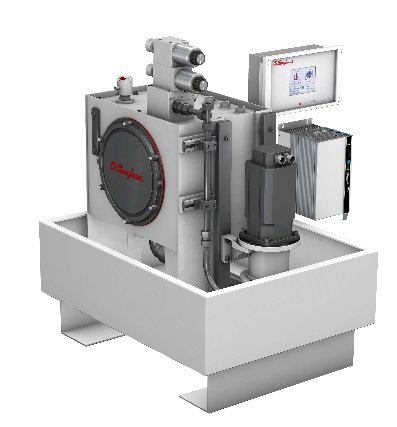
Pa.go enables the precise closed-loop control of clutch-brake units in large presses. While such control brings considerable benefits during normal operations, it also helps to counter the impact of changes in operating conditions like temperature, wear, oil leakage etc.
With Prop.act – our new shifting clutch system – we have taken another step toward the future. The hydraulically actuated, wet-running clutch unit with shaft end connections on both sides, integrated oil supply and hydraulic control can be installed on a ship as a ready-to-use compact unit. A stand-by pump is additionally installed, that keeps the system self-contained at any time.
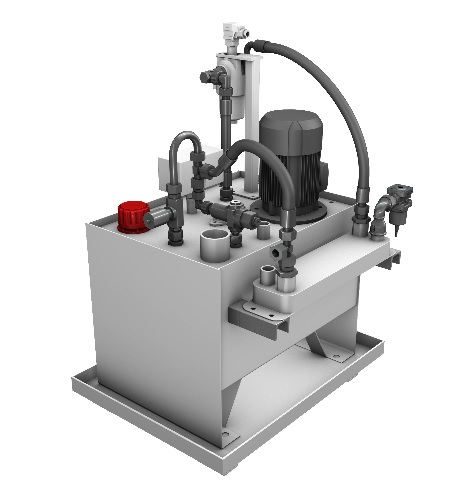
Ortlinghaus has been manufacturing single and multi-channel rotary inlets for several decades and these are frequently supplied as accessories for air and oil actuated and also for oil cooled clutches. These tried and tested machine components for the feeding of air, pressurised oil and cooling oil into rotating shafts are standard products and are not only for use in conjunction with clutches. In addition to this Ortlinghaus also develops and manufacturers rotary inlets to customers own requirementswhich cannot be met from standard products listed in the catalogue. It is thus possible for example to manufacture rotary inlets with up to eight channels with the channels being able to carry different media (air / oil; air / water).